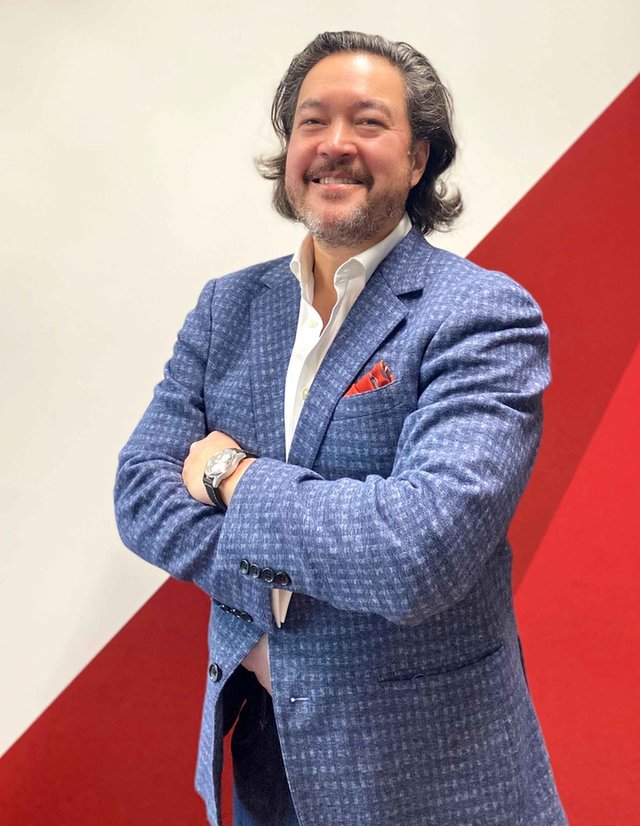
Dark Clouds are Gone. Time for Sunshine
We can’t wait until we find a new normal! How many times have you heard this hackneyed cliché in the past few years? Retail veterans should scoff at this comment, though, because they know that retail’s only constant is disruption. Change is the only normal. It is the pace of change that has infused additional strain into the system. So, what changes should we anticipate for 2023?
Digital transformation remains an elusive target, but a worthy journey. Retailers and brands will continue their pursuit to become more digital. However, there is no clear end goal with digitalization. Does it mean to have a better web presence? Social retailing? A mobile-first strategy? Greater usage of data and analytics? Establish a modern PIM solution? Yes, to all of the above. The ‘digital journey’ suggests that there is, in fact, a destination; but there isn’t, really. It’s a continual evolution to integrate digital tools into your core business processes in order to keep up with the digital consumer. In 2023, as companies emerge from the COVID fog, we should see a reassessment and reinvestment in digital technologies. Retailers will compartmentalize different digital efforts, from data usage and social presence to user interfaces and analytics; the one constant thread throughout that digital evolution is that it’s all about empowering retail to meet customer demand.
Retailers will double down on fulfillment in the quest for better customer satisfaction. Digital transformation will garner some of the headlines, but in parallel, the physical aspect of supply chain will continue to grow in importance when it comes to customer satisfaction. The pandemic accelerated e-commerce for many retailers and brands. However this has thrust greater pressures on supply chains and placed major strains on the physical aspects of logistics; being able to make, move and deliver items. As the calendar flips, supply chains must remain top of mind for retailers. Savvy retailers will double down on their fulfillment efforts that have been exposed during the pandemic. This involves looking into the different nodes of the physical supply chain — warehouse, distribution centers, logistics providers, stores — and evaluating how to better leverage these assets to meet your consumers’ expectations. It’s time for action; to make the necessary changes throughout supply chains, from new business processes to modern technology such as fulfillment robotics.
2023 should be viewed as a reset for retailers and brands, wherein they focus on key initiatives and address trends that do not require hand sanitizer, masks and social distancing.
An ESG focus will go beyond feel-good social media conversation and become a true change agent for retail strategies. Fulfilling orders efficiently and cost effectively are essential for customer satisfaction, but consumers will expect more from retail in 2023. 86% of global consumers expect business, and their leaders, to lead on societal issues. Consumers will vote with their wallets if retailers and brands do not meet their expectations. Expecting that brands have a social conscious is nothing new; I remember when consumers voiced distaste over Coca-Cola for doing business in an apartheid South Africa. Today, with the speed and openness afforded by social media, brands and retailers can neither hide nor feign ignorance when it comes to working with bad actors or not practicing good sustainable practices. Savvy retailers will not only focus on being good stewards of the environment but will also look to leverage this to create more customer loyalty. Retailers and brands can ignore ESG at their own peril, because their consumers will not.
2023 should be viewed as a reset for retailers and brands. The beginning of 2022 was still marred by COVID (remember the Omicron breakout?) with mask mandates and social distancing rules stretching well through the first part of the year. We have not irradicated COVID, but it appears that we have it under much better control. 2023 should enjoy the benefits of being the first year since 2020 that does not have to operate under the dark COVID clouds. That will afford retailers and brands the runway to focus on key initiatives and address trends that do not require hand sanitizer, masks and social distancing.